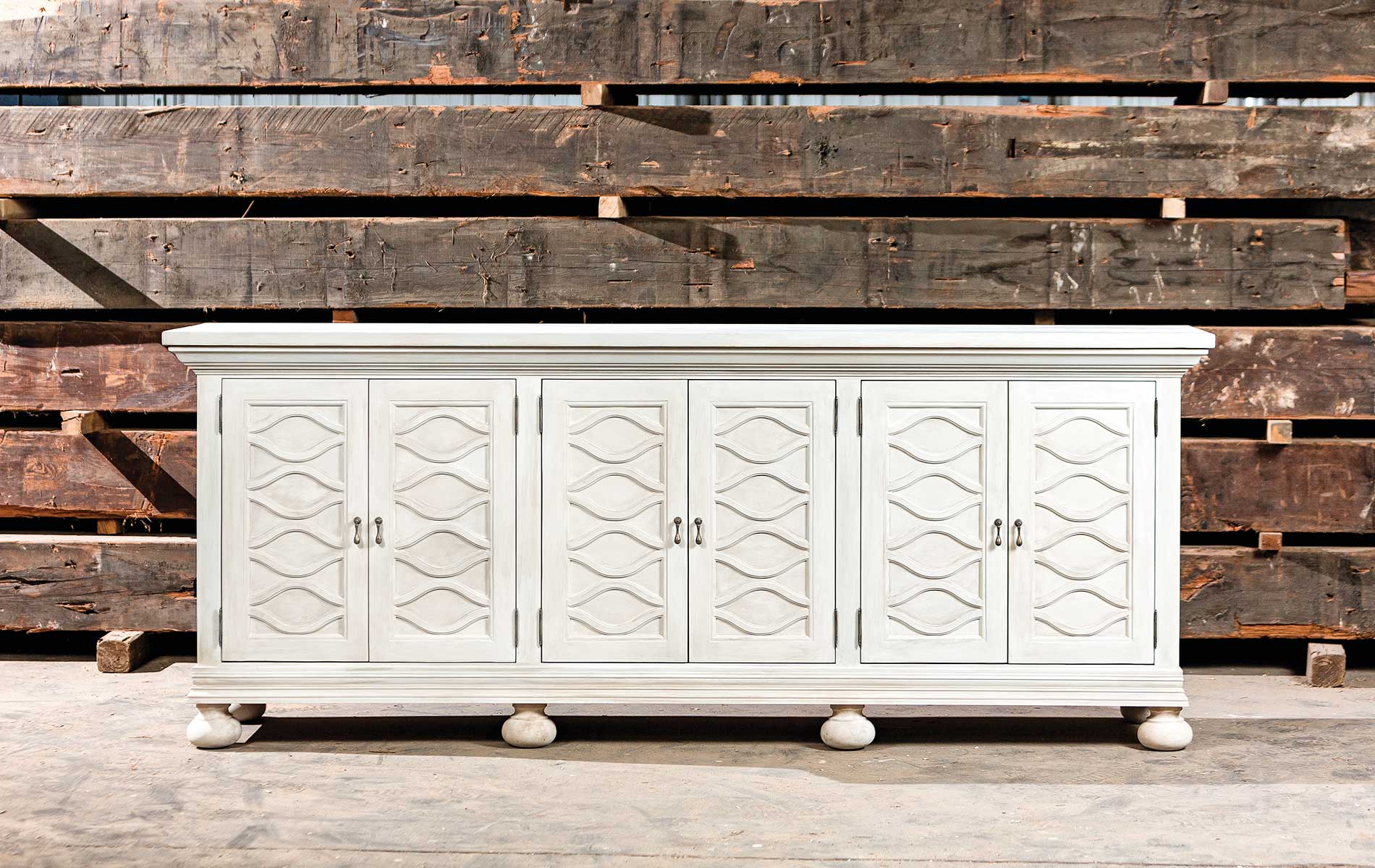
vie-magazine-armored-frog-feature
The Armored Frog
Sallie W. Boyles | Photography provided by Armored Frog
A few years ago, when Joe Sinkovich and his wife, Alicia, decided to settle in Pensacola with their young son and daughter, they fell in love with a house built in 1918. The place needed work, but they were fully committed to restoring the fixer-upper. When the renovations began, Joe was a sales and marketing executive designing orthopedic equipment for an orthopedic implant manufacturer and he traveled extensively. Therefore, Jimmy and Dusty McGraw, a father-and-son team who specialized in historic preservation, were in charge.
Considering that the structure was nearly a hundred years old, Joe anticipated some surprises along the way. When checking on the job’s progress one day, he encountered a twenty-foot-by-twenty-foot hole in the front wall. The sight of the hole was not remarkable, but the pile of rotten wood would ultimately send Joe on a journey—one that would totally reframe his world and quite a few others’.
It all began when Jimmy revealed that the damaged boards were from a 1970s addition. “The home’s original heart pine and cypress,” Joe explains, “were beautiful and seemingly untouched.” Thus, Joe asked Jimmy to rebuild the section with hearty old woods that matched the rest of the house. The straightforward remedy, however, presented a challenge: Jimmy had no sources for procuring antique lumber.
The old-growth heart pine and cypress that Joe desired comes from massive trees that stood for centuries. Maturing slowly beneath a thick forest canopy, the old giants developed intricate rings and extremely hard cores. Their high resin content further makes such woods resistant to damaging insects, which is why the end products—from barns to beds—have endured over time.
For many reasons, Joe’s favorite wood is Southern heart pine. “Straight and strong, it’s incredibly versatile,” he says. “The most common tree used in ship masts during the eighteenth and nineteenth centuries, the longleaf pine built the Southeast.” Many question his preference for pine because they are accustomed to the lumber currently harvested from eighteen-year-old trees grown on farms. However, the young, soft wood, which easily warps when exposed to the elements, cannot be compared to four-hundred-year-old pine cut from the heart of the tree.
For many reasons, Joe’s favorite wood is Southern heart pine. “Straight and strong, it’s incredibly versatile,” he says. “The most common tree used in ship masts during the eighteenth and nineteenth centuries, the longleaf pine built the Southeast.”
Despite clear advantages, the ancient wood comes with a price. From the mid-1800s to the 1930s, logging companies throughout the South took the trees by clear-cutting ninety million acres of irreplaceable virgin forests. Preservation laws help protect what remains, so users must rely on previously harvested old wood. Since supplies are limited and often difficult to retrieve, the material can be expensive.
Unaware of how much time and money he would invest to find and buy the preferred wood, Joe was undeterred. “I’m inquisitive and willing to make mistakes,” he says, indicating that in over twenty years of consulting with surgeons to meet their precise requirements, he has grown accustomed to researching and addressing complex matters. “If we’ve got a problem, my job is to find a solution fast,” Joe states.
While still working full-time in medical sales, Joe says, “I started calling builders for leads. None of them had suggestions, so I contacted some of the local cabinet shops and then people who specialized in renovating old houses.” Two months later, he located the wood.
“Twenty-five people in the Southeast buy old lumber,” Joe says. Much of it comes from old buildings—barns, houses, factories, etc.—as well as from riverbeds. Interestingly, the timbers recovered from Florida’s rivers are among an approximate 10 percent that loggers lost during the heydays. Every piece has a history; the logs are even branded, identifying the logging companies of yesteryear.
He had worked in that factory forty-seven years, so the old floor meant something to him—it represented the place that was central to his life and town. It occurred to me then that we save a piece of history every time we reclaim a piece of wood.
“From the start, I wanted to understand the origins of the wood and my role in its preservation,” says Joe, who vividly recalls the first time he went to a retrieval site. “We removed flooring from a textile plant in Alabama. Covered in dirt, I walked outside and met a man standing there with his little boy. He said, ‘Son, if I could tell you the number of times I walked across these floors!’ He had worked in that factory forty-seven years, so the old floor meant something to him—it represented the place that was central to his life and town. It occurred to me then that we save a piece of history every time we reclaim a piece of wood.”
Nostalgia comes with the job, but business is business. “Old wood doesn’t mean it is always good wood or workable wood,” Joe says. Citing factors like nails, paint, creosote, and even natural decay, he adds, “We’ll lose 30 percent of any log or reclaimed material.”
The “we” he refers to is Armored Frog, the company Joe founded two years ago while becoming an old-wood specialist. Procuring the lumber for his house highlighted opportunities for processing boards and making distinctive furniture. “Few suppliers are equipped to process the material,” he says, “and the majority of high-end heart pine and cypress is used for flooring and paneling, not furniture.”
Working initially from a shed, James, who went along with Joe, began building planter boxes and tables. Purposely choosing an esoteric name for the company, Joe pays tribute to the durability of the planter, crafted to contain the dirt (as he describes, “like an armored box”) and protect the vegetation. Likewise, the insect-eating frog is acknowledged as a friend of the tree and a welcome garden dweller.
Today, Armored Frog inhabits a 26,000-square-foot warehouse that resides on more than five acres of land. Joe fulfills multiple functions within the company—designing, selling, and managing the company—and employs a professional team of designers, craftsmen, and artisans. Jimmy is the production manager and a senior craftsman. Accordingly, the company has an estimated year’s worth of raw inventory in stock to meet a flourishing niche market’s demand for handcrafted old-wood tables, desks, and media centers. Styles range from rustic to modern.
More than seeking a certain look, Joe’s discriminating customer wants authenticity. That kind of buyer doesn’t think twice about paying $3,000 to $5,000 for a custom table. Most, in fact, are working with designers who have led them to Armored Frog. Presently, approximately a hundred designers throughout the country refer their clients to Joe. Understandably, expectations run high, but Joe and his team are the most discerning of all. The company’s motto, “Nothing leaves the shop unless it’s perfect,” stands without question.
About 90 percent of Armored Frog’s output is custom ordered, usually with a designer’s input. The average lead time is twelve weeks. “For the right price, we can stop everything to finish a piece in ten days,” says Joe, “but if it’s not perfect, I tell the designer to call the client and say it’s not ready. I’d rather return the money to an impatient buyer than have someone find a flaw, even if that happened a year or two later.”
To avoid mistakes, Joe first creates a footprint template on butcher paper that the customer can position in the space intended for the furniture. “They give me dimensions, but 50 percent of the time they realize the piece would be too big,” he says. Various finishing options—paint, stain, oil rub—also require some thought. “They want to match the rest of the room,” Joe says, “so color is important.” To gain ideas or to purchase an item in stock, some customers, accompanied by their designers, visit the warehouse. “They often end up staying for hours,” says Joe.
The equipment in action can be as mesmerizing as the array of finished furniture. Like the old wood, the machines are vintage and built to last. “Today’s standard saws are fine for cutting particleboard and veneers,” says Joe, “but not hardwood. My old saws are made of cast iron and weigh up to 4,500 pounds.” They also accomplish the job. Joe points to a 1973 Robinson resaw that can reduce a beam sixteen inches high by eighteen inches wide to furniture-grade boards within thirty minutes.
Exhibiting extensive knowledge after only two years in the business, Joe says, “You have to know where to find the right information with the right amount of time and money.” After visiting “every cabinet shop in Pensacola,” he turned to furniture manufacturers for guidance. Attending trade shows in Dallas, Atlanta, Las Vegas, and High Point, Joe claims that a handful of production managers in charge of high-quality, solid wood furniture operations provided all the insights he needed. “I asked them questions like what kind of glue were they using,” he says.
The one thing a successful person can do is to give others the opportunity to do well in life. My goal is to employ as many people as humanly possible. It’s so rewarding to train and develop people to make a living and to look back and say, ‘Look what we made.’ At the Armored Frog, it just so happens that we make furniture.
While willing to share their expertise and applauding Joe’s intentions to manufacture in the United States, they told him he’d never succeed by producing here. “The furniture plants in North Carolina, once the heart of furniture manufacturing, are shutting down and moving overseas,” says Joe. In addition to causing unemployment, that strategy, he believes, has left voids within the US high-end furniture market. Joe is happy to fill both gaps.
Armored Frog is a design, build, and finish studio. “We work closely with designers throughout the US to build one-of-a-kind pieces,” Joe adds. “Designers view us as a resource to help them deliver something special to their clients.”
— V —
Consumers can view past Armored Frog custom pieces online at armoredfrog.com.
Share This Story!
KEEP UP WITH THE LATEST STORIES FROM VIE